Onder Poeder lassen
Tosec heeft volop ervaring met en is gecertificeerd voor OP lassen.
OP lassen kenmerkt zich door een hoge neersmelt alsook een relatief hoge inschakelduur en dus een hoge efficiëntie.
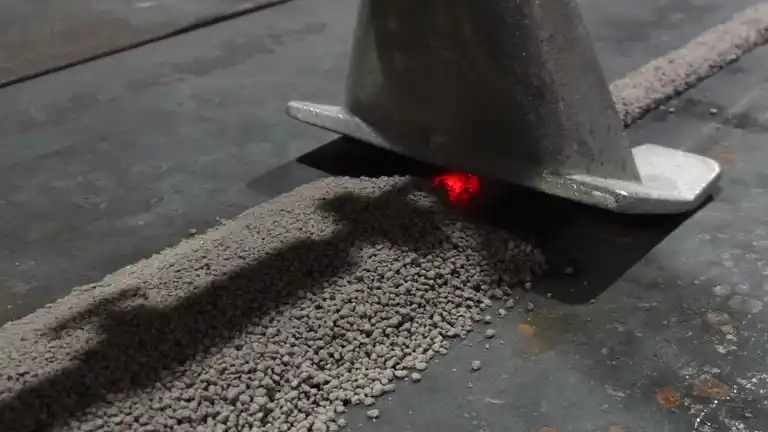
OP lassen - het proces
Bij OP lassen (Onder Poeder lassen) wordt een lasdraad continue met een vooraf ingestelde snelheid toegevoerd vanaf een spoel of vanuit een drum. Door een elektrische spanning tussen de draad en het werkstuk ontstaat een vlamboog.
Om de las te beschermen wordt continue en met een vaste hoeveelheid korrelvormige flux toegevoerd. De flux verbrandt deels waarbij het beschermgas ontstaat. Daarnaast ontstaat een slak die de hete las beschermd tegen invloeden van buitenaf en voorkomt oxidatie.
Internationaal staat OP lassen bekend als Submerged Arc Welding, of in het kort SAW.
OP lassen kenmerkt zich door een hoge neersmelt en diepe inbranding
Kenmerken OP lassen
OP lassen kenmerkt zich door de mogelijkheid om met zeer grote lasstromen te werken en daarmee een grote neersmelt te bereiken. De diameter van de gebruikte lasdraden loopt dan ook al snel op tot ø 4 mm of groter. Het is zelfs mogelijk om te lassen met strip om bredere lassen in slechts enkele lagen volledig te vullen.
OP lassen wordt vrijwel altijd geautomatiseerd uitgevoerd worden. Dit heeft als voordeel dat de lassen uiterst constant zijn.
Voordelen van OP lassen
- Hoge neersmelt
- Hoge inschakelduur
- Door automatisering, zeer constante kwaliteit
- Vrijwel geen nabewerking noodzakelijk, o.a. door uitblijven van lasspatten
- Door hoge stroomsterkte is een diepe inbranding mogelijk
- Door wijze van bescherming is de geluidsproductie veel lager alsook de uittreding van gevaarlijk UV licht
Nadelen van OP lassen
- Veel warmte inbreng (heat input) waardoor er krimpscheuren kunnen ontstaan
- Doordat het smeltbad niet zichtbaar is, is bijsturen van het proces minder eenvoudig
- Lassen kunnen alleen onder de hand gelegd worden i.v.m. de losse, korrelige, flux
- Minder geschikt voor complexe producten